Coal Fired Steam Boilers Manufacturing
The combustion process of coal fired steam boilers is mainly from coal scuttles fall in front of the grate, with the grate operation, the coal after preheating distillation, fire, burn, cinder into the slag bucket, by the slag removal machine. The pipe of the coal-fired steam boiler forms a eddy current in the penthos between the front and back arches to mix with the air fully and heat the front arches to improve the ignition conditions. It enters the left side or the convection tube bundle of the two wings through the non-outlet smoke window on the arch, enters the threaded smoke pipe through the side smoke box and the front smoke box, and is discharged from the induced draft fan to the chimney through the economizer and dust collector.
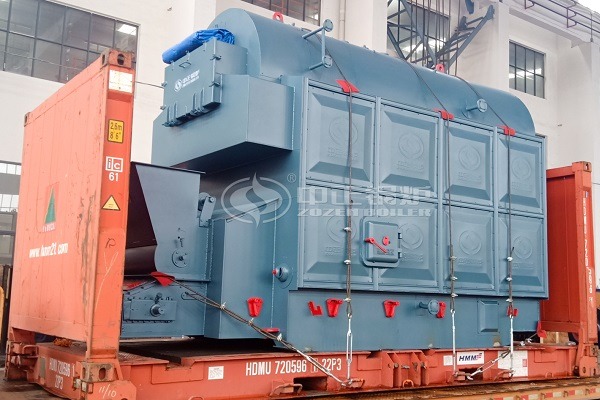
Coal-fired steam boiler
This series of steam boiler cylinder is arranged in the convection heating surface of threaded smoke tube, the front and back arch and furnace wall are made of heat-resistant concrete integral casting and ramming new technology, the boiler main body outside for baking paint three-dimensional protective plate shell. The structure of coal fired boiler body is tubular type, airfoil flue type, and the combustion equipment is divided into chain grate and reciprocating grate. The lower part of the boiler is arranged with a rising row pipe, which eliminates the dead water area at the bottom of the drum, so that the sludge is not easy to deposit, and the high temperature area of the boiler can be cooled well, preventing the lower part of the boiler from bulging. The heat transfer effect is enhanced by using the university heat transfer screw pipe, and the heat efficiency of the boiler is improved.
Coal-fired steam boiler compact structure, compared with the same type of boiler, the external size is small, save the basic investment of boiler room. This series of boiler is stable operation, convenient adjustment, full output, with 110%* load capacity. Steam boiler adopts threaded smoke pipe to enhance heat transfer, improve the heat transfer coefficient and thermal efficiency, because the flue gas in the pipe by the disturbance, smoke pipe is not easy to collect ash, played a role in self-cleaning. This series of boilers product adopt heat-resistant concrete integral pouring wall and vermiculite concrete outer wall protection layer, enhance the tightness of the furnace wall, reduce the air leakage coefficient of the furnace wall, avoid the impact of flue gas short circuit on the output and efficiency of the boiler.
This series of boiler furnace adopts heat-resistant concrete integral casting of the funny energy-saving furnace arch, improve the coal fire conditions, the use of the wind chamber, to achieve a reasonable distribution of air, so that the furnace formed a favorable combustion of the aerodynamic field, so that the adaptability of coal. The furnace arch, outlet chimney and tube bundle of this series of boiler products all have a certain function of dust removal, so that the original dust concentration of the boiler is controlled under the standard, ensuring that the flue gas emission of the boiler can meet the environmental protection requirements.
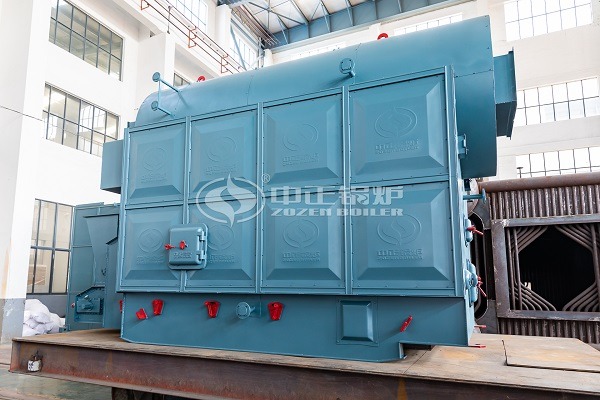
Coal-fired boiler supply
The normal water level of coal-fired steam boiler must be maintained during operation. Constant attention should be paid to working pressure to maintain it at normal pressure. Under normal circumstances, the pressure should be kept stable, and the high and low deviation should not be greater than plus or minus 0.05mpa. The prescribed working pressure of the boiler should be marked with red line on the pressure gauge of the boiler. Zozen Boilers specializes in the production of various types of boiler products, over the years we have reached a friendly cooperative relationship with customers from many countries, welcome you to come to our factory to consult and purchase, we will serve you wholeheartedly!
Leave a Reply