Oil Fired Thermal Oil Boiler Working Principle
The oil-fired thermal oil boiler can use a circulating oil pump to force the thermal oil to circulate in a liquid phase. The heat energy is transferred to the heating equipment and then returned to the heating furnace for reheating. It has the characteristics of low temperature and high pressure. In addition, it can output two or more heat transfer oils of different temperatures at the same time according to customer requirements. Therefore, it is widely used in petroleum, chemical, textile, printing and dyeing, plastics, food and other industries, and has been unanimously trusted and recognized by customers. The thermal oil boiler principle is simple, and its heating temperature can reach 300°C in the liquid phase or 400°C in the vapor phase.
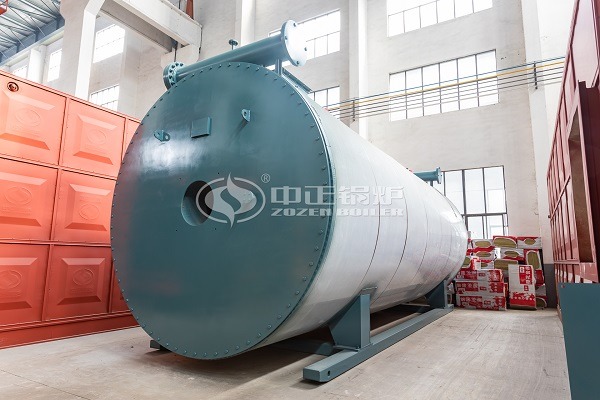
Thermal oil boiler principle
This series of thermal oil boilers have the characteristics of obtaining high working temperature under low pressure, and can control the operation of the medium with high precision.This boilers system has high thermal efficiency and is a kind of energy-saving heating equipment because of the overall installation of the module and convenient operation and maintenance. When the product is in operation, the fuel is ignited by the burner and the high temperature flame is generated into the inner coil, forming a radiation heating surface, and rotates 180° forward through the back of the inner coil, and enters the interlayer area of the inner tube and the outer tube, forming a convection heating surface. Then from the upper part of the interlayer into the interlayer area of the external coil, from the interlayer area behind the chimney into the atmosphere.
The thermal oil boiler principle is clear at a glance, and it adopts a horizontal three-pass structure, which is very compact. This series of boiler products have high system utilization, convenient operation and maintenance, and complete control system. Moreover, energy saving, environmental protection and safety are the first choice of ideal heating equipment at present. Oil fired thermal oil boilers can be widely used in petrochemical, textile, printing and dyeing, plastics, rubber, food, wood processing, asphalt heating, carton production, vegetable dehydration, baking varnish, casting sand mold drying and other fields.
The oil fired thermal oil boiler adopts a digital display temperature controller to control the temperature. It has the functions of over-temperature alarm, low oil level alarm and over-pressure alarm. Although the working pressure of the thermal oil furnace is relatively low, the temperature of the heat transfer fluid in the furnace is high, and most of them are flammable and explosive. Once leakage occurs during operation, it will cause fires, explosions and other accidents, and even cause casualties and property loss. Therefore, we must attach great importance to the safe operation and management of organic heat carrier furnaces. Because it has the advantages of high temperature (above 320℃) and low pressure (0.3-0.5MPa), and its heating temperature can be controlled, it can replace the original steam boiler for heating. At the same time, the equipment does not require water treatment equipment and there is no heat loss such as running, emitting, dripping, and leaking of the steam boiler, so it saves one-time investment and low operating costs. It is a safe, efficient and energy-saving heating equipment.
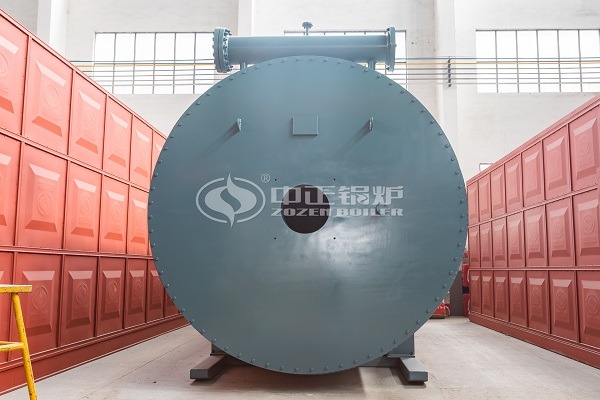
Oil-fired thermal oil boiler
The thermal oil boiler principle is simple, and the heat transfer oil is directly heated by the heat source. And through the high-temperature oil pump for liquid phase circulation, the heated heat transfer oil is transported to the heating equipment. Then return to the thermal oil furnace from the oil outlet of the heating device for heating. This forms a complete circulating heating system. In some industries, the boiler is gradually replacing traditional steam boilers with its unique advantages. Although the working principle of the oil-fired thermal oil boiler is relatively simple, we still have to pay attention to its use during the use process.
Leave a Reply