Manufacturing Processs of Industrial Gas Fired Steam Boiler
The gas-fired steam boiler adopts an advanced full-wet-back, flue gas three-pass horizontal fire tube structure. The fuel is combusted in the furnace with slight positive pressure. The high-temperature flue gas enters the first flue tube bundle through the re-combustion chamber backward along the furnace, and enters the second tube bundle through the compressed front smoke box by 180°, and is discharged into the second tube bundle after convection heat exchange. The atmosphere has a high thermal efficiency (greater than 95%). The gas boiler manufacturing processs adopts a high thermal resistance fiber-enclosed metal outer casing as a thermal insulation layer, which has good thermal insulation performance. Because of the integral steel structure base, the installation is very convenient.
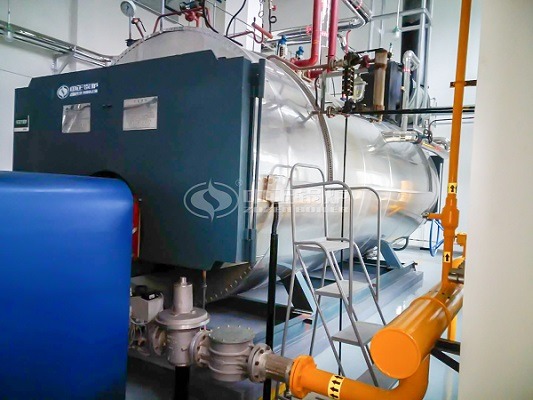
Gas boiler manufacturing processs
The gas-fired steam boiler adopts a three-pass full-wet back design. During operation, the fuel is injected from the burner into the 100% water-in-water fired furnace to burn. The furnace is surrounded by water, and flame and high-temperature flue gas flow from the front to the back of the furnace, forming the first return. The high-temperature flue gas flows to the front through the back-combustion chamber, passes through the second-return smoke pipe to the front smoke box to form a second return. Then it flows through the third return smoke pipe to the rear boiler flue gas outlet to form a third return. Use high-performance wave furnace, the furnace is at the bottom of the boiler water. The industrial gas boiler has a large furnace volume and many radiant heating surfaces. The flame has a high degree of fullness, the flue gas flows naturally and smoothly, and the combustion efficiency can reach more than 99.5%. Therefore, the amount of harmful components produced is small, the structure is more reasonable, and the service life is long.
The gas boiler manufacturing processs uses a multi-unit multi-return tube pass design. This design enables the flow of flue gas to achieve high-speed turbulent flow, preventing the occurrence of tube blockage. And strengthen heat transfer, reduce back pressure, and improve heat transfer efficiency. At the same time, a large-capacity steam storage room is designed to be able to deal with load fluctuations, pressure instability and peak changes in time. It also provides high-quality dry steam to eliminate the generation of extra condensate and prevent scaling inside the boiler. The use of labyrinth double-sealed smoke box prevents the leakage of smoke and the local temperature of the smoke box is too high. The heat loss of the boiler is minimized, and the airtightness is excellent.
This series of boiler products have advanced manufacturing technology, advanced testing methods and reliable quality. The WNS series boiler smoke tube adopts the advanced technology of pre-expansion and then full welding, which not only prevents tube crevice corrosion, but also enhances the welding strength. The multiple safety protection design ensures that the boiler body can expand and contract freely under temperature and pressure changes, and the thermal stress is extremely low. There is a manhole on the top of the boiler, which can be entered into the boiler for inspection, repair and maintenance. There are two hand holes symmetrically distributed at the bottom of the boiler for easy inspection and cleaning of the bottom of the shell. The boiler smoke box is equipped with symmetrical movable hinged front and rear smoke box doors, which is convenient for opening, checking and cleaning.
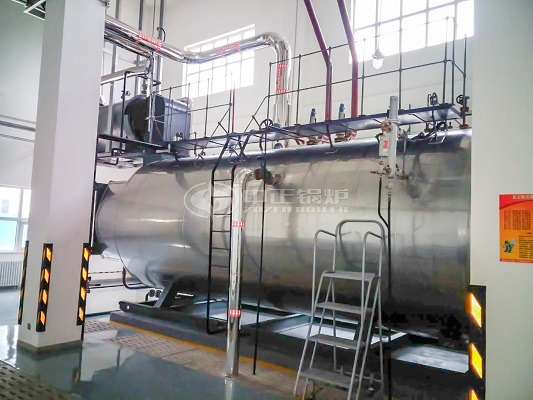
Gas-fired steam boiler
The manufacturing level and testing methods of industrial steam boilers are advanced. In accordance with the prescribed standards and industry standards and the requirements of the company’s quality assurance system. It adopts automatic welding, radiographic and ultrasonic testing. Various production and inspection methods such as hydraulic test are done before leaving the factory. And the special equipment safety supervision and supervision department supervises and inspects the whole manufacturing process to ensure the high quality of the products.
The gas boiler manufacturing processs has excellent, and the high standards of the exhaust gas produced by the boiler fully meet the specified requirements. This boiler adopts a fully automatic burner. The boiler load is controlled by the pressure controller to control the size of the fire or adjust the fuel injection volume in a proportional manner to meet the load requirements. It also has the function of overpressure automatic shutdown protection. At the same time, the operation of this series of boilers adopts a digital intelligent control system and a fully automatic control system. With simple operation, the boiler automatically completes various signals such as pre-purge, detection of water level, pressure, temperature, and fuel gas leakage. Automatic ignition, adjust the size of the load, fully automatic operation. Ensure that the safe operation of the boiler is always under control.
Leave a Reply