Diesel Fired Boiler Efficiency is Generally How Much
Diesel steam boiler is favored by users, in addition to its environmental protection and energy saving, there is an important advantage, is high thermal efficiency. Diesel fired boiler efficiency is high, not only can save fuel costs, but also an important embodiment of environmental protection. So, what is the general thermal efficiency of oil and gas boiler?
In fact, the thermal efficiency of diesel steam boiler can not be generalized. Because the thermal efficiency of boiler products produced by different models and different manufacturers is different. As a result of boiler design, structure, fuel texture, management factors, stoker technical level and quality and so on. Diesel fired boilers in practical application, thermal efficiency will also have a great difference. The operating cost of the boiler will also vary, depending on the specific situation.
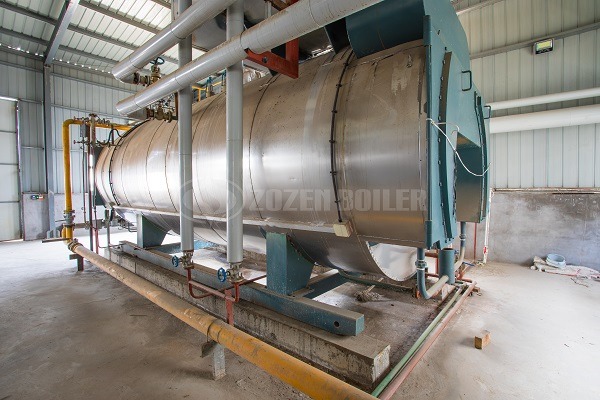
Diesel fired boiler efficiency
The diesel fired boiler efficiency is more than 95%, which is an automated boiler product developed by ZOZEN’S and Xi’an Jiaotong University. The structural performance of this series of oil-fired boilers is at a leading level. Many environmental protection countries require high boiler exhaust gas emission standards in areas that choose to use this type of diesel boiler, which is environmentally friendly and energy-saving. Zozen Boilers continues to absorb advanced foreign technology, combined with domestic actual needs, to develop new technologies. The oil-fired boiler developed by our factory has high thermal efficiency, sufficient output, high combustion rate, large heating surface, low exhaust gas temperature and low heat loss. The boiler equipment produced is spread all over the world and is well received by users.
Diesel boilers mainly use diesel as fuel. Fuel oil is a liquid fuel, and its boiling point is always lower than the ignition point. Therefore, the combustion of fuel is always carried out in a gaseous state. After the atomized oil particles are sprayed into the furnace, the fuel is heated by the high-temperature flue gas in the furnace for gasification. The vaporized oil and gas meet the oxygen in the surrounding air to form a flame. Part of the heat generated by the combustion is transferred to the oil particles, so that the oil particles continue to gasify and burn until they burn. The smaller the diameter of the oil particles, the faster the burning of the oil particles. Similarly, the oxygen required for the combustion of oil particles is supplied in time, and the oil particles burn faster. Therefore, to strengthen the combustion of oil, it is necessary to improve the quality of atomization and reduce the diameter of oil particles. Increase the relative velocity of air and oil particles. The boiler is equipped with reasonable air distribution.
The longitudinal axis of the horizontal diesel boiler shell is equal to the ground and the combustion chamber is contained in the body. This series of boiler burner nozzles are placed in the front of the furnace, and the high-temperature flue gas produced by combustion extends to the rear. After leaving the furnace, it returns to the space (return chamber), and enters the second return journey (smoke pipe) after near return. Such as turning back once, it is called a two-return boiler. Such as turning back twice, it is called a three-pass boiler. By analogy, the general number of turn-backs does not exceed four, and the most common is the three-pass boiler.
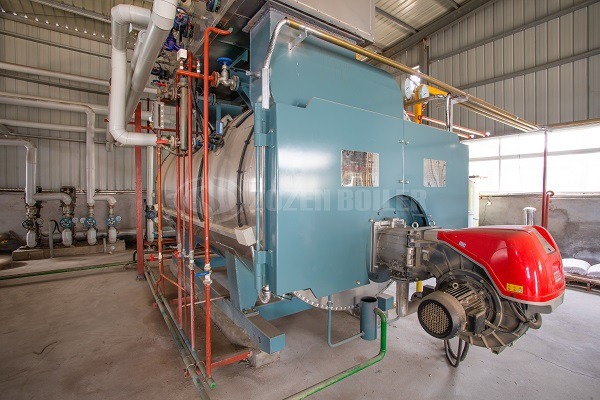
Horizontal diesel boiler
The improvement of diesel fired boiler efficiency can shorten working time, reduce combustion consumption, and save operating costs. Oil-fired boilers have been developed rapidly as a new environmentally friendly boiler product, and they have the advantage of environmental protection and clean pollution. The auxiliary equipment of this series of products has a computer control cabinet, which is the control system of the boiler. It has virtual buttons, LCD screen, and electronic operation manual. We only need to press the button to fully control the boiler.
Leave a Reply